As Kitply workers roll up their sleeves to develop India’s first formaldehyde free Plywood, Mr Gaurav Goenka, Chairman, Kitply Industries Mr Gaurav Goenka, Chairman, Kitply Industries Ltd in conversation with Mr Pragat Dvivedi, Founder, Ply Reporter & IIR divulges some intriguing details pertaining to the edible resin used in making of this exclusive product. Proclaimed as safest plywood to use in interior grade panels, the product might have the potential to revolutionize the premium interior design segment.
Q. You are actually based in Kolkata, so what drove you to acquire the plant here in Ambala?
Kitply has a pan-India presence and the North region has always been in the front of our retail focus area, therefore we seized the opportunity of acquiring this Ambala plant three years back. Now for the last two years we are in full production here and evolving continuously. It is in the DNA of our company right from my forefathers time that we are accustomed to do something path breaking. So following the same spirit and line of thought we have come up with this new plant.
Things we are doing here in Kitply are going to lay the foundation of a resilient future of the plywood industry in the same manner as electric vehicles are revolutionizing the automobile industry. We are fortunate to have successfully developed this new technology here in India, which has long been in practice globally.
Q. Kindly elaborate on this new Resin technology that you have introduced in the Kitply plant?
Right from my formative years I had this firm conception that making plywood without formalin is impossible but if one cares to research a bit, formaldehyde is classified as category 1 carcinogenic according to WHO. Therefore we took concern and worked on it to make the process more environment and health friendly. We came across a company called Solenis which has developed this edible resin, used in many packaged food items. To our amazement, the same resin has been used to build bio plywood.
Q. What about the build quality, do you think this edible grade resin renders the same strength to Plywood as conventional formaldehyde?
Yes, definitely, globally this product is approved for interior grade projects. Despite any ISI standard testing facility available in India, we have tested it on the basis of USFDANAF (no added formaldehyde) in our internal laboratory to attest that the product is perfectly suitable to be used in the Indian interior design industry. We have seen that this biotech adhesive is actually very sturdy and thick in comparison to usual PF and UF resins because on bonding it with Soya it takes long to settle due its high density. Hence, there is no remarkable difference between normal plywood and resin bond plywood in terms of strength. The product is called Kitply BioBond; it is India’s first formaldehyde free bio based panel product that is made organically for strong bonding of the ply.
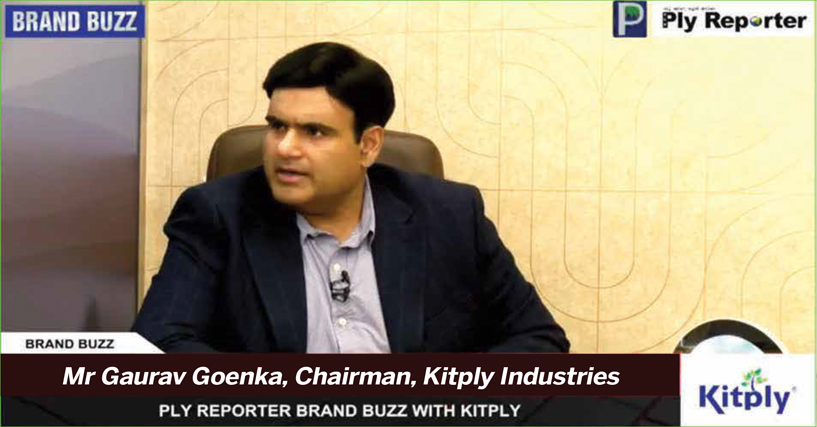
Q. We also look at E0 and E1, producing the similar category of plywood, so how will you distinguish Bio Bond Bio Bond?
That is a product category but take for instance the automobile sector, currently we are following BS 6 standard, earlier it was BS4 but electric vehicles don't have any such emission standards because the technology is completely different from combustion engines. Similarly the difference lies in technology altogether so our bio-bond is India’s first formaldehyde free product, it is the future. After having gone through three four rounds of trials, the product is ready for the market and we will be launching it in next quarters.
Q. When we develop plywood applications of this sort, it's open in public and anyone can recreate it, so how do you keep it discreet?
Sure, moreover we would like the whole industry to follow the trend but there is a catch in it. Actually the biotech glue which is used in the process is developed by Solenis and the company had patented the resin. We are in agreement with the company to launch it in the Indian market, so no one else can procure it from Solenis in India.
Q. Does Solenis have any plant in India producing the resin for Bio-bond?
Solenis is a 4 billion dollar company with plants in Ankleshwar Gujarat, though initially when we tried the product, the first batch of trials happened in the US only but now we are procuring it from Gujarat only. Apart from this Soya flour needed to extract the resin is also being sourced from one their vender company in India only.
The mixture generally contains water, termite resistant formula and other additives that are generally used in the plywood manufacturing, we have just replaced the UF or PF resin with FDA based glue.
Q. Where else in the world this product is currently being used? Do you think Indian consumers are ready to accept the product yet?
From the US to Europe, the product has been widely accepted, they have already created more than 100 million ply boards using the same technology, though the technology has come a little late in India owing to lack of health awareness in India.
Given the fact the product is going to be priced at a slightly higher price compared to our premium plywood because of the incorporation of so many modalities, one cannot put a price tag on the life of an individual. As the awareness among Indian consumers pertaining to hazardous industrial products is increasing, the product will soon find its niche in the domestic market as well.
Q. Being the only producer making such exclusive bio based Plywood, how do you predict the response of Interior Designers, Architects and Retailers?
Like any other new product that comes in the market, it takes a while to find its niche, for instance calibrated ply came 10 years back but now a well accepted product in industry, Bio Bond will be a path breaker particularly in the household interior applications as people are now very much aware of health hazards besides it will also offer a favorable environment for workers in the factory.
Q. Health hazards are certainly an alarming concern in plywood factories, how healthy is the working environment at your factory?
You ought to see for yourself the environment inside the factory as during our trials all our workers felt that this environment should permeate across the whole plant. This technology emits no obnoxious fumes, detrimental to their health. Even after the product is ready and consumed at any interior project’s site, carpenters and clients need not worry about the fact that product might cause any adverse effect on their health.
I will speak on behalf on the whole industry, over a period of time many organized players are shifting towards creating brand, cause with the increase in the purchasing power of India, people are getting brand conscious even in the building material segment and we are poised at a very good position to take it forward in terms of our market share.
We have expanded the team rapidly in most of the zones, which we constantly review on a monthly basis. There is always a scope for expansion, for which we have created a roadmap internally to target around 100 new cities where we have limited or no presence at all. We want that as a consumer.
Q. Shall we expect more new products from Kitply in near future?
Yes, it is very much in our thought process to launch new products and ultimately if you intend to remain in the frontrunners of this industry, the only way is to develop multiple quality products. But right now our focus is on the primary product that is Plywood and we are determined to re-establish it.
Kitply will assert itself with its innovative spirit, reaching out to more than hundred cities in future, it is gratifying to see that one more organized player is establishing itself with a vision of a sustainable future.
The man behind developing the amazing edible resin, Mike Kahnle of Solenis talks about working in India with Kitply and their ingenuity to develop such an exclusive product in the interest of healthy environment.
Q. You must have visited dozens of plywood plants at multiple locations in India Mr Mike; do you see any scope of improvement?
Yes, I have visited many plants across the globe and the Kitply plant to me is actually an astounding manufacturing facility, the equipment and the people who are working in the plant are every bit better than many of the places that I have been in the past. Both management and employees are skilled enough to run the operation smoothly.
Q. Let us know the market share of this Resin technology in the rest of the world?
Let me enlighten you that this Resin technology has already been used by many countries across the world. In the United States for example the sixty per cent of the plywood is being manufactured for interior grade panels by using our product. In Europe we have number of manufacturing plants who are using our products and have literally produced more than 100 million over a period of the last twenty years.
As far as the difference in the resin is concerned, being a food certified resin; it is completely safe and free from formaldehyde. If you look at the global health, we use 50 percent less petroleum products and hence contribute in reducing the carbon footprints through consuming less of the fossil fuels.
We are trying to do something which is brand new in our industry with a healthier and better product not just for the workers here but consumers and carpenters who use it at home. We drain the soya flour and food grade resin which is found in your coffee filter or napkin. From this concoction we will develop an adhesive to bond the ply. This celery with a viscosity over 45000 cps is spread over the Veneer through splatter than rest of plywood operation is followed in usual manner.
“If one cares to observe the texture of this bio bond plywood, there is no top dipping done in its making, its a natural form even from the edges, the product is termite free and comes in BWR grade with no gaping. Buyers can easily do the quality check by scanning the code at the hologram,” informs Sunil Arora of Kitply.
With this formaldehyde free plywood, Kitply has ventured to step ahead of E0 and E 1 grade ply, if company manages to establish this new product by driving awareness among retailers, distributors and consumers about the noble objective behind launching it then its usability will surely overreach pricing because there is nothing more precious than a healthy life.