The one-day seminar on ‘Market Acceptance of New Face Veneer and Future of Plywood Industry’ was organized by The Ply Reporter in association with Greenply Industries Limited in Jalandhar, Punjab on 9th June 2018. The seminar was attended by more than 100 plywood manufacturers of Punjab.
After the successful completion of three consecutive TalkOfTheTown series seminar on ‘Market Acceptance and Need of Okoume Face Veneer’, The Ply Reporter organized its 4th seminar in Jalandhar, Punjab on June 9th 2018 in association with Greenply. Mr Pragath Diviedi welcomed the august gathering and eminent personality from the industry and threw light on the objective of the seminar. The programme was moderated by Mr Rajiv Parashar, Managing Editor, The Ply Reporter.
Addressing the audience Mr Pragat Dvivedi said that people want to have option of Gurjan face but they are in fear as the dealers still focus on Gurjan face. He said about this initiative and the purpose of the series of seminar which is going on in the country. In consequence to research on the subject, the industry feedback reveals that face availability of Gurjan and other species except Okoume is constraint which is becoming big trouble for the industry players/manufacturers.
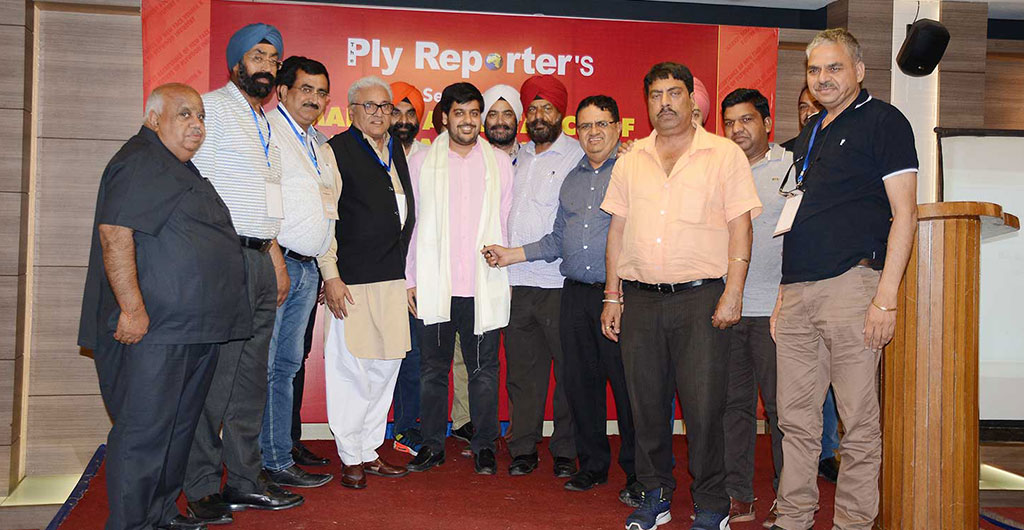
He further said that Greenply is always ready and open to all to make the industry learn this method and the R&D they have done and achieved a cost effective and better solution for ply-boards as an option to Gurjan. If they can shift their total ply-boards operation on Okoume and saving a lot, then everybody can benefit with it. “Gurjan face input cost in plywood manufacturing is around 22% today, but Okoume face cost is 6 to 8 percent maximum. This vast saving due to different sustainable face adoption can be invested in other area of operation in the industry. And with all industry players move towards the industry will benefit with it in multiple way. With this objective we have done this seminar in Yamunanagar, Bareilly, Cochin and now in Jalandhar, because if the industry gets united can benefit more in this regards,” he added further.
As the team Ply Reporter and Greenply have made commendable efforts to organise manufacturers to this point, if they have included leading dealers and wholesalers in this efforts, the success rate to this initiative would have been 100 percent right from the beginning. You must be aware that Okoume import to ICD (Inland Container Depot) Ludhiana and Delhi has reach to over 60 containers per month, which is a big boost.
Mr Naresh Tiwari, Chairman, AIPMA heartily congratulated the Ply Reporter and Greenply for their initiative to spread the knowledge and awareness among industry players which can benefit with its cost effectiveness and sustainable availability. Addressing the audience he said, “Okoume is a substitute of Gurjan. When we first came to the industry in the year 2002, that time people were talking that this is the future and next life to the plywood industry. That time it did not do well because the availability of Gurjan was in plenty. Now Indonesia, Malaysia and many other Gurjan rich countries have no availability of it. Today the Greenply’s technical team has invented a solution to made Okoume face like Gurjan. You must be aware that Okoume import to ICD (Inland Container Depot) Ludhiana and Delhi has reach to over 60 containers per month, which is a big boost. The reason to the boost is non availability of Gurjan and other similar face and whatever is available, is of low quality.”
Greenply has been using Okume on its entire range of ply, boards and doors and it is well accepted in market. There is no quality related issue of using Okume face and it is available sustainably in market with affordable pricing. ‘Dealers, Architects and users are not been hesitant of using Okume faced make plywood, hence everyone should start using okume because it will help to save your money and survival’.
He further said, “As the team Ply Reporter and Greenply have made commendable efforts to organise manufacturers to this point, if they have included leading dealers and wholesalers in this efforts, the success rate to this initiative would have been 100 percent right from the beginning. If we see the back stage talking among industry people, they are still hesitant to use Okoume. Greenply has their mission to make learn their industry pears right from their beginning in the industry are doing commendable efforts in this regard also.”
Secondly, he said that he had warned manufacturers’ as well that 18 mm ply-board is facing competition from MDF and Particle Board as their manufacturing is huge and ply board rate is not going down but other products rates are going down sharply, ultimately the effect of MDF and PB will goes on Plywood manufacturing. And that time by way no other option manufacturers will have to use Okoume.
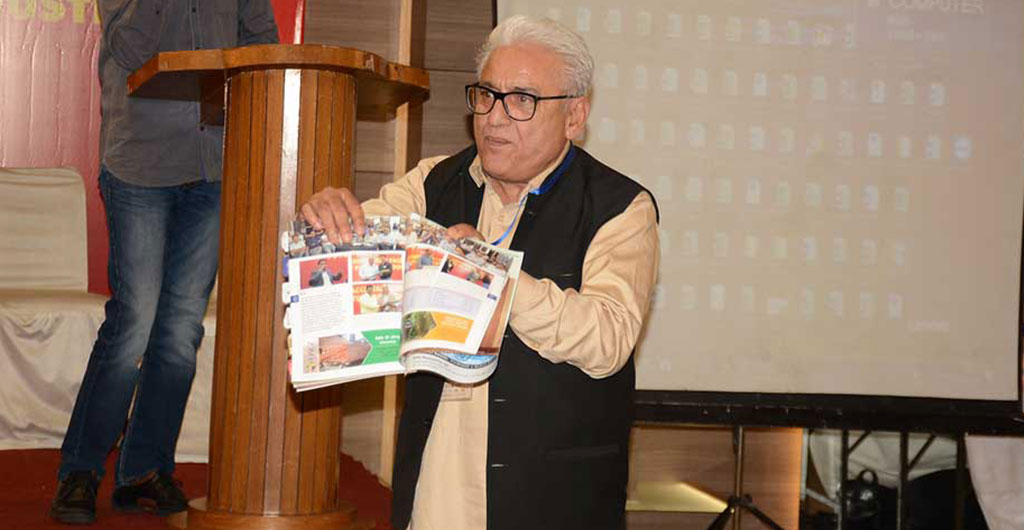
Addressing the audience, Mr. Ashok Juneja, Chairman, PPMA appreciated the effort of The Ply Reporter and Greenply for driving such awareness program for using economical grade Face veneer option which would help the industry and trade in future.
Addressing the gathering Mr. Sanidhya Mittal, Executive Director, Greenply confirmed that Greenply has been using Okume on its entire range of ply, boards and doors and it is well accepted in market. There is no quality related issue of using Okume face and it is available sustainably in market with affordable pricing. He also said, ‘Dealers, Architects and users are not been hesitant of using Okume faced make plywood, hence everyone should start using okume because it will help to save your money and survival’.
From the technical team of Greenply, Mr Praveen Choudhary said that Okoume is the best option as its characteristics has to accept the colour in better way. It comes in pinkish red and some part in white colour, which can be treated easily to obtain Gurjan like colour or whatever you want. The advantage of Okoume is being legal and no issue of unavailability in future other than the supply from Laos, Indonesia, and Malaysia. The second advantage is not having oil content in its face as in Gurjan with increasing temperature (as generally happen in summer seasons) it releases oil and increases the staining problem in manufactured product. Due to being oil free Okoume inventory can be stocked in good manner. The water resistance quality makes good quality ply board with 100 % Okoume face. Okoume is borer and termite free also. It has some issue related to colour variation which have been solved by the Greenply research team and after that Greenply has shifted their total operation on this specie and doing well in the market with having advantage of low input cost products with good availability of Faced ply board.

Mr Girish Sharma, another technical professional from Greenply briefed about the dipping and colour correction methods and offered its solutions to eradicate patches and un-uniformity of colour after dipping. “Okoume has three grades C, D and D2. D2 has heavy knots and heavy discolour so that is used separately. But C and D is for ply board in which 20 percent face is white coloured which do not show much change in colour after dipping. But, to get this problem solved we invented a dying solution after an extensive R&D,” he revealed.
Gurjan face input cost in plywood manufacturing is around 22% today, but Okoume face cost is 6 to 8 percent maximum. This vast saving due to different sustainable face adoption can be invested in other area of operation in the industry. And with all industry players move towards the industry will benefit with it in multiple way.
“We increased the glue viscosity which fills the porous surface of Okoume face and offer even surface after filling it with similar colour to Gurjan,” told Mr Girish. He also given practical presentation through video for dying and dipping process and promised to give practical operation at several manufacturing units in the city as open house for the industry experience to ply board manufacturers.
For Dipping & Dying the technical team of Greenply used brown pigmentation with its formulation as below:
Formulation for Dipping treatment:
► Copper Sulphate 3.8 %
► Sodium Dichromate 3.6%
► Chromic Acid 1.1%
► Brown Pigment 0.3%
► Red Pigment 0.05%
► Black Pigment 0.02%
► Godrej Ezee 0.05%
Formulation for Dye Pigmentation:
► WATER 11.5 Litters
► Brown pigment 0.665 Litters
► Red pigment 0.050 Litters
► Black pigment 0.275 Litters
To make Dye Solution with above formulation in to the 1000 Litters of water
Mr Pragat Dvivedi, Founder Editor, the Ply Reporter moderated the panel discussion on the topic, which was participated by Mr Naresh Tiwari, Mr Sanidhya Mittal, ED, Greenply, Mr Vishal Juneja of Vidhata Industries, Mr Lucky from Golden Plywood; Mr Praveen Choudhary from Greenply (Gabon operation). Industry people queried about the quality, sustainability, grading and availability of Okume Face Veneer, which was well replied by Mr. Sanidhya Mittal and Mr. Choudhary of Greenply. Mr. Inderjit Singh Sohal, President, PPMA thanked all manufacturers for attending the seminar as well as Greenply and Ply Reporter for organising this for the future of plywood industry.