With the change of time and the ongoing trend of Matt finish laminates, the perception of consumer demand for such laminates in the market has now evolved towards such product offerings which look premium. In different niche market segments, the focus has now leaned towards the imitation of luxuries creating the perfect balance of comfort and elegance.
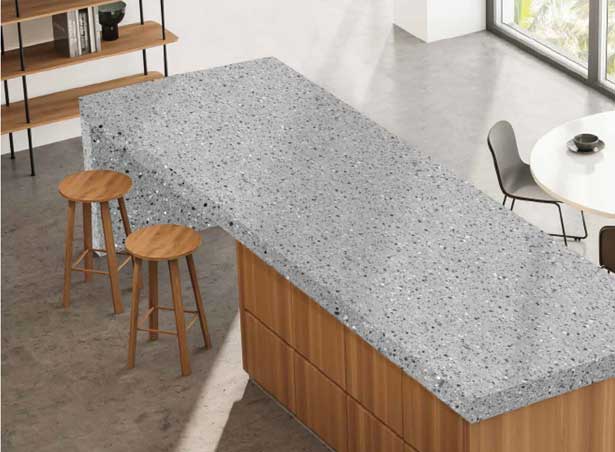
While Gloss surface finish has been in fashion for the last couple of years, the trend & demand for a zero gloss surface finish is gaining momentum. Matte finish produces an elegant, softness to the surface. It also provides a softer, more natural look.
In view of which, the company had introduced 10 SKUs in the 2021-22 Collection of Greenlam Laminate, however due to the overwhelming demand and feedback from the market on the expansion of the range. Greenlam reworked on the range and introduced 41 new designs in Satin Finish, with an overall offering of over 51 Designs.
GREENLAM SATIN- PREMIUM LAMINATE COLLECTION
A finish that exemplifies a characteristic of being smooth, soft – to – touch in nature, available in stunning Colours, Patterns & Wood designs. In the new offering there are 12 decors in wood designs with 8 patterns & 31 décor colours.
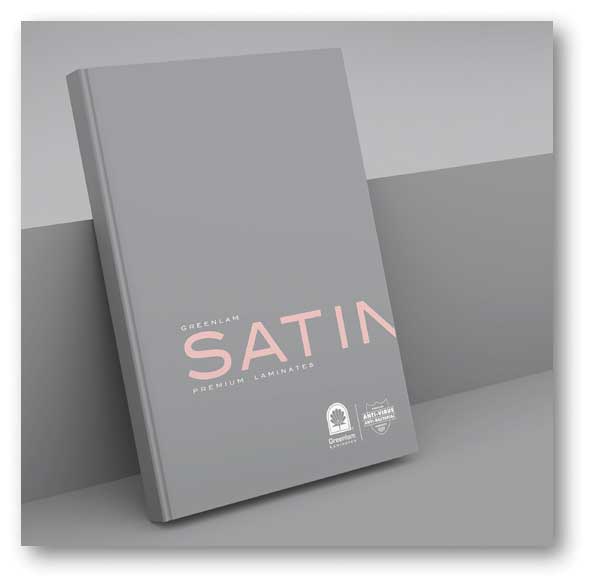
WOODS: These sophisticated woods designs offer the best of both worlds, beautiful designs in a soothing, matte finish without sacrificing performance.
Available in 12 Decors, with medium pore design, this even-textured wood finish adds just the right amount of expression to your surface.
PATTERNS: Ideal for High-Touch areas throughout any space. This collection includes elegant designs with authentic tones and touchable textures.
Available in 8 Decors, these designs offer a more realistic view of the stone or patterned laminate, versatile enough to pair with any interior design concept.
COLOURS: Designs which imparts a warm, pleasing effect that enhances the beauty of color and produces great clarity and depth for any application. Available in 31 Decors, these solid colors give unprecedented design and redefine the aesthetic beauty of interior decorations.
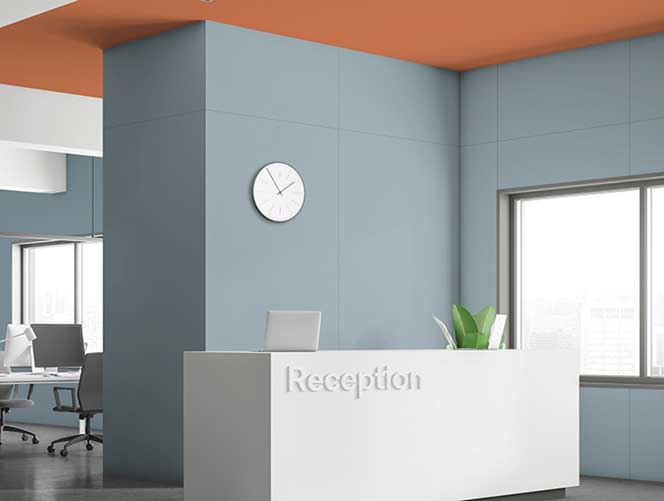
Besides, being Super-Matt, the range also comes with the added features of being Anti-Virus, AntiBacterial, Heat Resistant & offering a 10 Years product warranty* (T&C as applicable).
Greenlam Satin Collection defines its own way to make the surface look niche and premium. Captivating every touch with its silky and super matt finish, there is simply no match to its designs.