Says Mr. T. K. Salim, Managing Director,
Greenland Particle Boards Pvt Ltd, Perumbavoor, Kerala
Kerala based Greenland Particle Boards Pvt Ltd is well equipped manufacturing unit of Rubber based Particle Board, having 150 cubic meter capacity per day. The plant has having all modern machineries showing the vision of its Managing Director, Mr. T. K. Salim, who has diversified into Panel manufacturing with proper research on technology and products as well. The Ply Reporter team recently visited Greenland Particle Board unit and interacted with Mr. Salim, whose vision is to produce quality boards and has taken proper care to their workers and staff in most organised way.
Q How did you enter into wood panel manufacturing business?
A Perumbavoor is known for plywood, saw mills, block board, and veneer units. In and around Perumbavoor at least 600 plus plywood, veneer and saw mill are functioning. One can always see veneer waste and the core left over of these plywood units plying on the road to various red brick factories and rice factories, where these are used as fuel for their boilers and furnaces. When enquired about the prices of these left overs; it was negligible and some units where giving it free of cost to clear their factory compound. After some research we came to know about particle board (chip board). In year 2008, after in depth research and visits to various particle board industries in different countries I tried to understand the future and the market potential of the same, which gave confidence to starting one particle board unit. The company was registered in the year 2010 in the name of Greenland Particle Boards Pvt Ltd, unfortunately the project took 5 years to take off, for reasons beyond our control.
Q What is your entire manufacturing infrastructure?
A We have altogether one lakh square feet of built up area in 4 acres of land with only one entry and exit point. Our installed capacity is 150 CBM. But we produce nearly 4,000 mother boards a day (24 hours) which is nearly 30% more than the installed capacity. Our production line is from Sufoma which belongs to the Chinafoma group company. The chip preparation section was build in excess capacity considering the future for extra production. We produce different thickness such as 9 mm, 12 mm, 15 mm, 17 mm, 18 mm, 25 mm and 26 mm low density filler boards. We have three short cycle lamination press out of which one is fully atomised and the capacity is 3500 prelam boards per day.
Q What skill is required to run a Particle Board plant in such limited area of land?
A Land is very expensive in Kerala knowing the fact that we have only 4 acres, the first and foremost thing was to plan the layout, and we believe that our layout was planned in such a manner which will fit a 150 CBM plant as well as all other amenities including staff quarters required for a clean and hygienic particle board unit.
Q What are specialties of your manufacturing process and products?
1. The raw material used in our manufacturing process is of one single species of wood which is rubber, which gives uniform density spread across the board.
2. The urea formaldehyde Resin is of 65% solid with a viscosity of 60’’ flow in B4 cup, which gives a very good spread and high bonding strength.
3. A very high Quality waxemultionhg from Govi Chemicals Malaysia is used in our manufacturing process with a solid content of 62%.
4. The hardener (Ammonium Chloride) used in our plant is imported from Shandong Kaiteda Chemical Company Ltd, China and the same is of pharmaceutical grade with 99.5% purity.
5. As far as the surface quality of our mother board is concerned we use 50, 100 and 150 grit sanding belt from Hermis, Germany.
Q Why did you opt for Particle Board whether because this area is known as plywood manufacturing hub?
A The basic reason for opting particle board is because particle board is the future until and unless a replacement for the same at reasonable price range is invented.
Q How sustainable is the timber supply for your particle board unit?
A As long as rubber is grown abundantly in the state of Kerala and being rubber a cash crop hopefully the supply of raw material shouldn’t be a problem in the near future.
We have altogether one lakh square feet of built up area in 4 acres of land with only one entry and exit point. Our installed capacity is 150 CBM but we produce nearly 4,000 mother boards a day (24 hours) which is nearly 30% more than the installed capacity.
Q Would you see further capacity addition in PB manufacturing in this region?
A Already there are three particle board manufacturing units in Kerala including ours one more is coming up in Palakkad. Some more might come up in the future.
Q Would you plan to enter into plywood, MDF or other wood panel manufacturing in coming years?
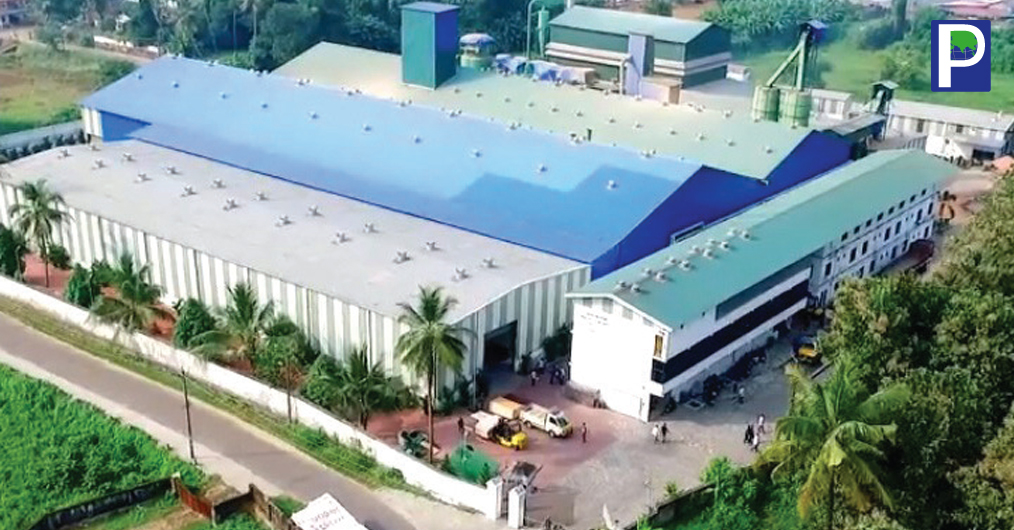
A Presently there is no plan to enter into anything if at all there is something it would be particle board only and the size would be 8X6. Because more big OEM’s will be entering into the knockdown furniture Arena and they would prefer the above said size to minimize wastage.
Q How rubber wood is suitable material for panel production if we compare with Eucalyptus and Pine?
A The only demerit in rubber wood is the latex content but we do have a unique round screen system which is able to arrest the latex lumps from reaching the flaker. All the OEM’s enjoys Rubber wood based particle board because it is very smooth while cutting in a panel saw or a beam saw and the blade used in a panel saw gives more than double the output in comparison to pine wood based particle board because of the silica content in pine wood makes it very hard to cut.
Q What is the perception of big OEMs about rubber made particle boards?
A Most of the big OEMs prefer 8X6 sizes, still some of them are very happy using rubber wood based particle board ignoring the fact of the wastage because they enjoy their life of blades.
Q What value added products are you offering?
A As far as the value addition is concerned other than wide range of decors, we offer digital designs, 3D and we are offering colour matched PVC edge banding and transparent glue of high quality to our clients.
Q How do you see the future of panel made furniture market in India?
A As in developed countries like Europe and Gulf the uses of knock down furniture will definitely increase day by day. The awareness of the same will increase so many folds with the arrival of IKEA.
Q What impact do you see of 28 percent GST of wood PB?
A The GST of 28% in wood based particle boards is in the higher side in comparison to baggase based particle board which is at 12% and the both are used by the same end users. We expect the central government to reduce the tax rate at least by 10% from the existing rate of 28% in the near future.
Q If bagasse (sugarcane) based PB is in 12 percent why not rubber based?
A Baggase based particle board is in the 12% bracket being an agro waste. Rubber wood being a cash crop there are several notifications considering rubber as agro product. As we are using only branches and the rubber waste we are entitled to get tax reduction. We are actually planning to move the goods and services tribunal Bangalore for the same.